

80° drum-turner
To make the production process safer and more efficient, the part within the installation where the drums are turned is automated. Large, heavy drums that may vary in height, are filled and fitted with a lid. They are then moved by a conveyor and must be turned upside down before they can be finally closed (pressed). This reversal is automated by a drum turner.
The drum turner is designed according to the position of the drums to be turned, the installation space, the drums themselves and their maximum weight.
Because this usually has to be done in-line, the available space is, of course, limited, and the height of the supply and removal conveyors is also limited to allow the operators to work ergonomically. This makes it impossible, for example, to place a machine next to, under or at the top of the conveyors that are powerful enough to safely reverse the drums. A drum perpendicular to the transport direction with a conveyor above and below is the best solution. However, the vessel must be locked up so that it does not fall during rotation. In addition, the drums must be clamped concentrically to allow them to be neatly turned around their centre of gravity (to limit the drive power of the rotating drum). In addition, both the upper and lower conveyor in the drum must connect to the transport level. An integrated clamping device that rises between the rollers is necessary.
Given the often large masses, safety must also be kept in mind. No dangerous situations may occur in the event of a breakdown or emergency stop. The vessel must always remain securely clamped. The drum turner offers a solution for a large - synchronized - power development with minimal installation space and attention to the safety of the employees and the installation.

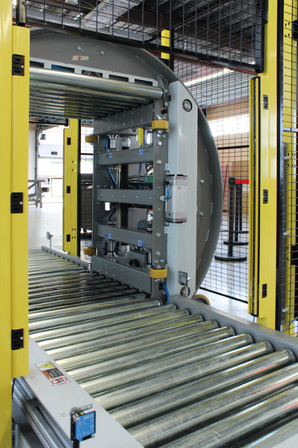
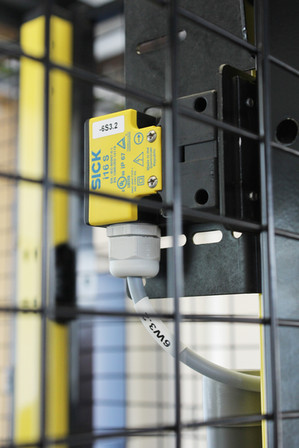

